Prof. Dickey’s Guide Through the Surprising World of Liquid Metals
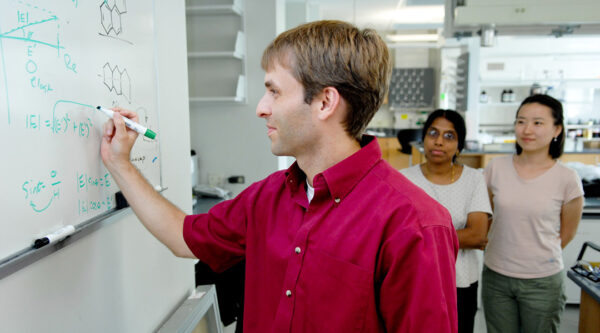
This is a modified version of an article originally published in Advanced Science News by Victoria Corless.
Prof. Dickey delves into the versatile applications, surprising properties, and future possibilities of liquid metals. He is seeking new ways to pattern, move, and control soft materials.
The overarching goal of his work is to study materials with “remarkable” properties that can be applied to areas like energy harvesting, sensing, memory, stretchable electronics, and robotics. What sets his work apart is an emphasis on simplicity, cost-effectiveness, and scalability, making these advancements accessible to a broader spectrum of industries.
One captivating aspect of his research revolves around liquid metals. As their name implies, these are metals that exist in a liquid state, the most well-known example being mercury — but as he’ll soon tell us, there are others. Dickey hints at a promising future for liquid metals, suggesting potential breakthroughs in self-healing electronics, batteries, and even catalysis. In this interview, Dickey takes us through the surprises, challenges and untapped potential of these materials (with visual aids along the way), providing insights into their evolving role in materials science.
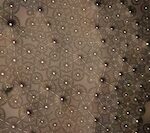
What are liquid metals?
When people say “liquid metal”, they’re really talking about a metal that’s a liquid at a reasonable temperature. The most interesting thing is the fact that it reacts — and not in a dangerous way — with oxygen to form a solid oxide on its surface. Think of it kind of like a water balloon or a water bed, in which this oxide layer not only protects the metal from additional reactions, but it also forms a self-healing skin only a few atoms thick that allows you to make shapes out of the liquid metal.
Aluminum, which we have in our kitchens, is also very reactive. But it is safe to use because, like gallium, it also forms an oxide layer that protects the inner, reactive part of the metal. Yet unlike aluminum, gallium remains a liquid on the inside of the oxide skin. We use this solid skin to control the shape of the liquid metal. The importance of the oxide becomes apparent by dissolving it away using acid or base. In that case, the metal beads up into a sphere. Also, if you put them into elastic materials, like rubber for example, you can make wires that are really stretchy.
Can they be made solid again too?
There’s a trick to keeping liquid metals from freezing, which is to mix them with other metals. Just like water on a cold day, if you don’t want it to freeze you add in salt. You do the same thing with gallium, it’s just instead of adding salt, you add other metals, like indium, zinc or tin, which depresses the melting point, allowing it to remain as a liquid at room temperature.
There’s a family of metals and metal alloys — we call them metal alloys because they contain multiple metals — that are liquids at or near room temperature. What they have in common is the fact that they contain gallium, a nice low-toxicity alternative to mercury.
What’s interesting about the oxide layer?
You have a liquid that normally flows like water, but then it naturally forms a thin solid shell on the surface. We have mostly used the oxide to help pattern or shape liquids into useful shapes, but there are other potential applications. For example, what if you could separate that oxide from the liquid? Then the liquid provides a source for creating oxides, which are important in electronic devices, gas sensors, and barrier materials.
There’s a number of ways to deposit oxide films on surfaces, but they typically use big, expensive vacuum chambers that require elevated temperatures. Such processes are slow and there’s just a bunch of challenges. But if you could just separate the oxide directly from the liquid, you could do it at room temperature — just imagine it being like a snake peeling its skin, but where the skin is valuable.
The oxide layer is very thin and it also has potentially useful properties. As an example, a touch screen like the one on your cell phone or your laptop, uses a thin oxide called indium tin oxide. What if you could deposit that from liquid metal? Could you could make conductive films in a really simple way? These are things researchers are thinking about.
What are some challenges to working with liquid metals?
This material never ceases to amaze and surprise. While we consider the oxide a desirable feature of liquid metal, there are cases when researchers prefer the metal to be free of oxide. Sodium hydroxide is a base that dissolves the oxide away. Likewise, certain acids will dissolve away the oxide as well.
Here, there’s no oxide anymore and you can see the effects of the large surface tension. Some people would suggest that the high surface tension of the bare metal is a challenge, but whether it’s a good or bad thing just depends what you’re trying to do. If you’re trying to recycle your material, this is great, because if you remove the oxide, your metal simply beads up and you can completely recover it. But if you’re trying to make a catalyst and you want to make really high surface area, well, this is a challenge because liquids prefer to minimize surface area.
We discovered something that I think is kind of mind blowing. If we apply a voltage to the metal in a pH-basic environment, you would expect the voltage to drive a chemical reaction called oxidation,

which should deposit oxide on the surface, and nothing interesting should happen. But instead when we do this, the liquid metal’s surface tension decreases. We know it drops because instead of being a sphere, gravity causes it to spread into a puddle. This is wild because under certain conditions, we think the surface tension is effectively 0. Not only does it spread, but it actually forms fractals, like a snowflake.
In another example, if you pump liquid metal out of a nozzle, it will form droplets like water out of a faucet. But if you start applying a bit of a voltage and drive these reactions on the surface, we find the droplets get smaller and smaller. When we reach the voltage where we see those fractals, we can get a cylinder the size of a human hair. We found the tallest container in our lab and made the longest, thinnest liquid metal wire we could. This is all a roundabout way of answering the question: sometimes there are things that might be considered a challenge and then someday you just stumble into something like this and it provides new research directions.
How are liquid metals used to make self-healing materials, such as self-healing wires or electronics?
Liquid metal droplets can be thought of as a water bed, but one where the skin is very thin. While it can break easily, it can also reform. Researchers have used this property to make self healing wires, which are wires that you can cut and put back together or, even better, cut, and they autonomously heal to retain conductivity.
For example, we’ve demonstrated self-healing, flexible electronics by coating fabric with the liquid metal. To do this, we make very small particles of the liquid metal, just simply by stirring it — that’s it; really, really easy.
When we dip a fabric into a solution of the particles the fabric becomes covered with this dense, yet thin coating of the particles. Surprisingly, it’s not conductive unless you “squish” it, which just breaks that oxide layer (like rupturing water balloons) and the liquid metal merges together to form a conductive circuit.
Then, if you come with a pair of scissors and you cut your material, you should reasonably break the circuit. But when you do cut through it, it stays conductive because where you’ve cut, those particles have actually merged together.
You mentioned the possibility of creating stretchable barriers? Where did this idea come from and what are they for?
Typically, stretchy materials are not very good barriers to gases or liquids. The reason that they’re stretchy is that the molecules or polymers in the stretchy materials can move around very easily. This same property makes it easy for gas molecules to diffuse through the material. So there’s usually this trade off with permeability and stretchability. Potato chip bags use a layer of aluminium to help keep the chips fresh, but these coatings are not stretchable.
What we did is was ask, “Why don’t we combine rubber with a liquid metal?” Because the metal is a good barrier to gases, we reasoned that we could make a stretchable barrier material for the first time ever by combining the metal with rubber. Why would you do that? Well, then you can make things like stretchable batteries for use in wearable electronics.

Currently, batteries have these rigid containers because you don’t want the liquid inside of them to come out and you don’t want the oxygen from the outside air to go in because it would destroy the battery. But the liquid metal allowed us to make this protected, stretchy battery, which is something nobody’s been able to figure out how to do yet. We just took advantage of the combination of the unique properties, that’s kind of the theme here.
What do you see as a promising development in your field, made by either your group or your colleagues?
This is just one person’s opinion, but I think in terms of applications, the lowest hanging fruit is likely in electronic devices. Companies are starting to take note. But in the academic space, one of the more interesting areas is taking advantage of the reactivity and the catalytic properties of liquid metals to drive chemical reactions in new ways.
Liquid metals are interesting because solid products don’t stick to them. For this reason, they’ve been applied in reactions such as CO2 reductions, which is a big thing these days. There is some work that I contributed to modestly, but was led by my friends Torben Daeneke and Kourosh Kalantar-Zadeh in Australia. They showed that you could use liquid metal to convert CO2 into solid carbon. Solid carbon is desirable because it’s easy to store rather than pumping CO2 underground, which could lead to potential leaks. Unlike gases, solid carbon is easy to store, just like charcoal.
Normally when you have a metal catalyst and you form solid carbon, it will stick to the catalyst’s surface and render it useless. So, it did its job by driving the reaction, but then the solid carbon kills the catalyst for future use. But solid carbon doesn’t stick to liquid metal, it actually exfoliates and is easy to separate it from the liquid.
This interview transcript was edited for flow and clarity